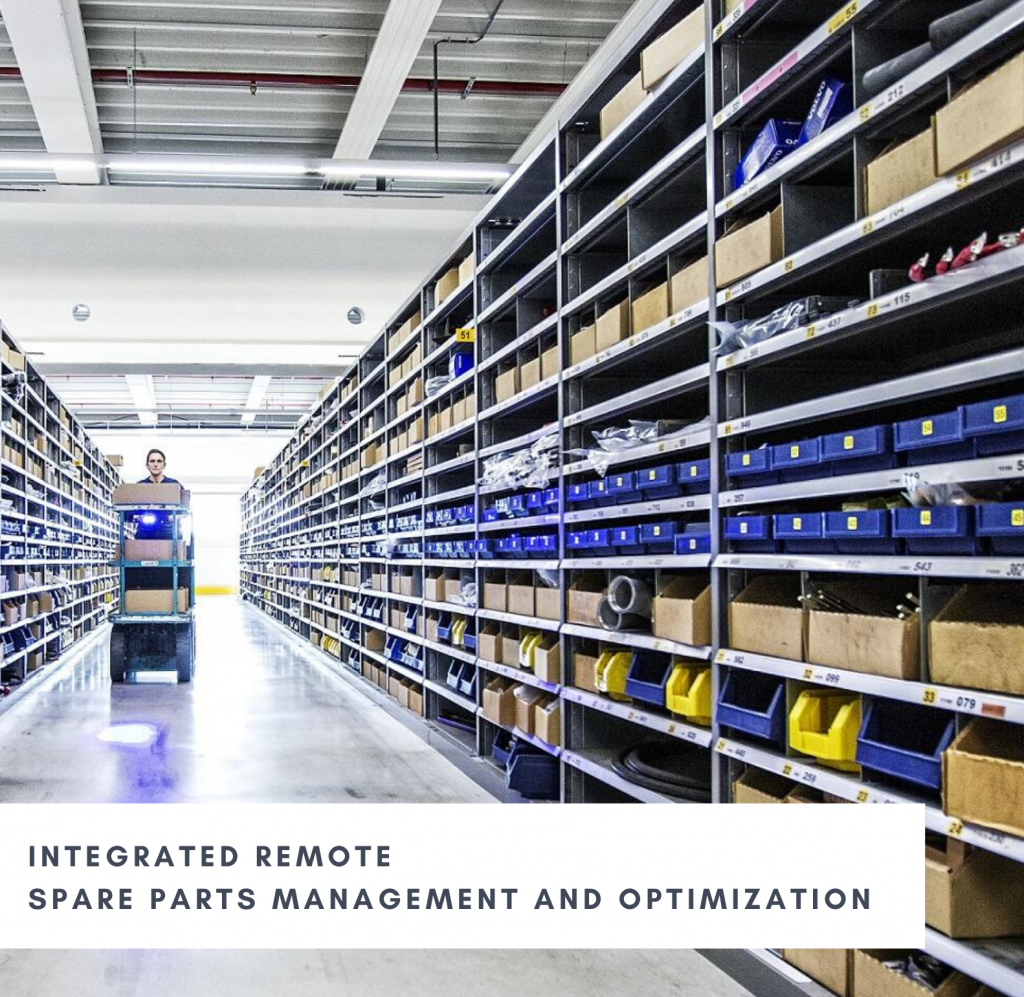
Spare Parts Procurement Prediction and Challenges :
Due to the increasing pressure for remaining competitive in the global market place, Vessel performance optimization has become a major challenge of Shipping companies. Unanticipated outages on board vessels can cost serious money. In fact, unplanned downtime for a ship can end up costing up millions per year for a Shipping company. The treatment of spare parts in shipping industry is different to that in traditional inventory management as they are neither intermediate nor final products to be sold to end users. The insufficiency or unavailability of spare parts can lead to long vessel downtimes or disruptions in the voyage. Moreover, storing extra spares may incur significant carrying costs, their degradation, or other warehousing issues. In addition, Procurement in spare part management is not always straightforward and is very challenging to predict. The challenge then becomes to effectively coordinate the overall inventory so the optimal amounts are maintained.
Spare parts management and optimization with Condition bases remote monitoring:
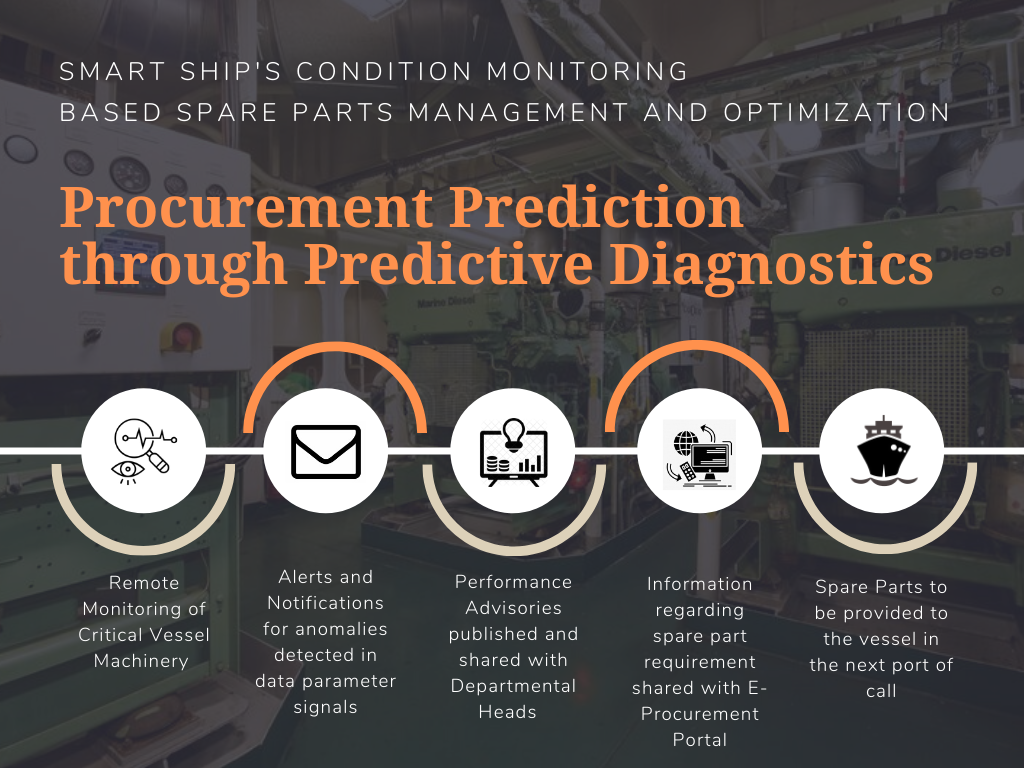
Smart Ship© Hub’s Remote Condition-based monitoring coupled with predictive diagnostics and maintenance collects real-time information on the healthy status of critical vessel machineries like Bridge, GPS, Echosounder, Rudder Angle, AMS, Main Engine, Lubrication System, Fresh Water System, Boiler, Ballast Water System, Fire Alarm System, Incinerator, Sewage Treatment Plant, Cranes, Cargo Monitoring System and Scrubber system etc. Smart Ship Hub’s Diagnostics Dashboard then continuously monitors the live data which allows for a more accurate estimation of the remaining life of Machinery or its parts, as well as provides Alerts, Notifications and advisories for a potential failure of a machinery part which may result in delays and down-times in the voyage of a vessel, which could again translate into additional cost and penalties.
Smart Ship brings also in integrated e-procurement platform which digitalizes the complete procurement process with the help of technologies like AI and Predictive Diagnostics. The data captured through the diagnostic dashboard regarding the faulty parts or the parts that are required to be repaired or changed is shared with the e-procurement portal automatically which in turn connects the vessel owners with the spare parts suppliers online for e-procurement of the spare parts.
The digitalization of the procurement process ensures :
- Better Inventory Management – with reduced inventory, warehousing, and overhead costs associated with inventory storage, labour and energy costs.
- Transparent tracking of Vessel Spare parts – minimizes errors associated with manual processes, as well as help plan cost control by providing accurate, real-time information on inventory levels.
- On demand “ Spares & Parts procurement” – based on machinery health ensures decreased stock of parts
- Improved demand forecasting – With the help of technologies like Artificial Intelligence and Machine Learning algorithms Smart Ship can help you move from traditional spare part management to more informed spare part forecasting model.
Smart Ship Pte. Ltd.
75 Meyer Road, #13-03 Hawaii Tower, Singapore
Singapore: +65 9894 6598 | India : +91 7620 225 640
Email: contact@smartshiphub.com
Singapore | India